The Design Process
Before hands and machines begin crafting the components that make up Budnik Wheels, our minds are hard at work creating designs tailored to meet your needs and complement your automotive creations. We are honored and deeply grateful when you choose our products for your remarkable rides.
It all starts with imagining the cars we admire. What would the perfect wheel design look like for that car? How big should it be? What finish would suit it best? We begin with countless hand-drawn and mental sketches before transitioning to our CAD system, where we draw each design to scale and refine it further. Our goal is to create designs that are fresh and unique—sometimes even nodding to the past with a retro-inspired, lightweight twist, crafted using modern materials, sizes, and finishes.
By blending creative ideas with our deep expertise in machining and wheel design, we produce wheels that are not only uniquely stylish but also lightweight, strong, and easy to clean.
Raw Materials
Forging the centers. Aluminum is such a wonderful thing. Maybe you’ve seen how brilliantly a polished Budnik wheel can shine. Well that’s just one of the benefits of our process and material. Our high quality forged American aluminum combined with the skill of our polishers (and certainly not a porous lower strength casting) creates a brilliant shine.
You can also see our signature forging profile. We've design our proprietary forging dies to give us just the profile we want on the face and variable brake clearance pads on the backside. You can get up to 2″ of big brake caliper clearance, without having to use spacers.
What you can’t see is the strength obtained by this hydraulic aircraft forging technique. During this method of forging, requiring a 4000 ton press, the molecular structure of the aluminum is re-arranged to increase it’s strength and even create a radial grain flow which is ideal for a wheel. Each wheel center is then heat-treated to T6 specs before machining begins.
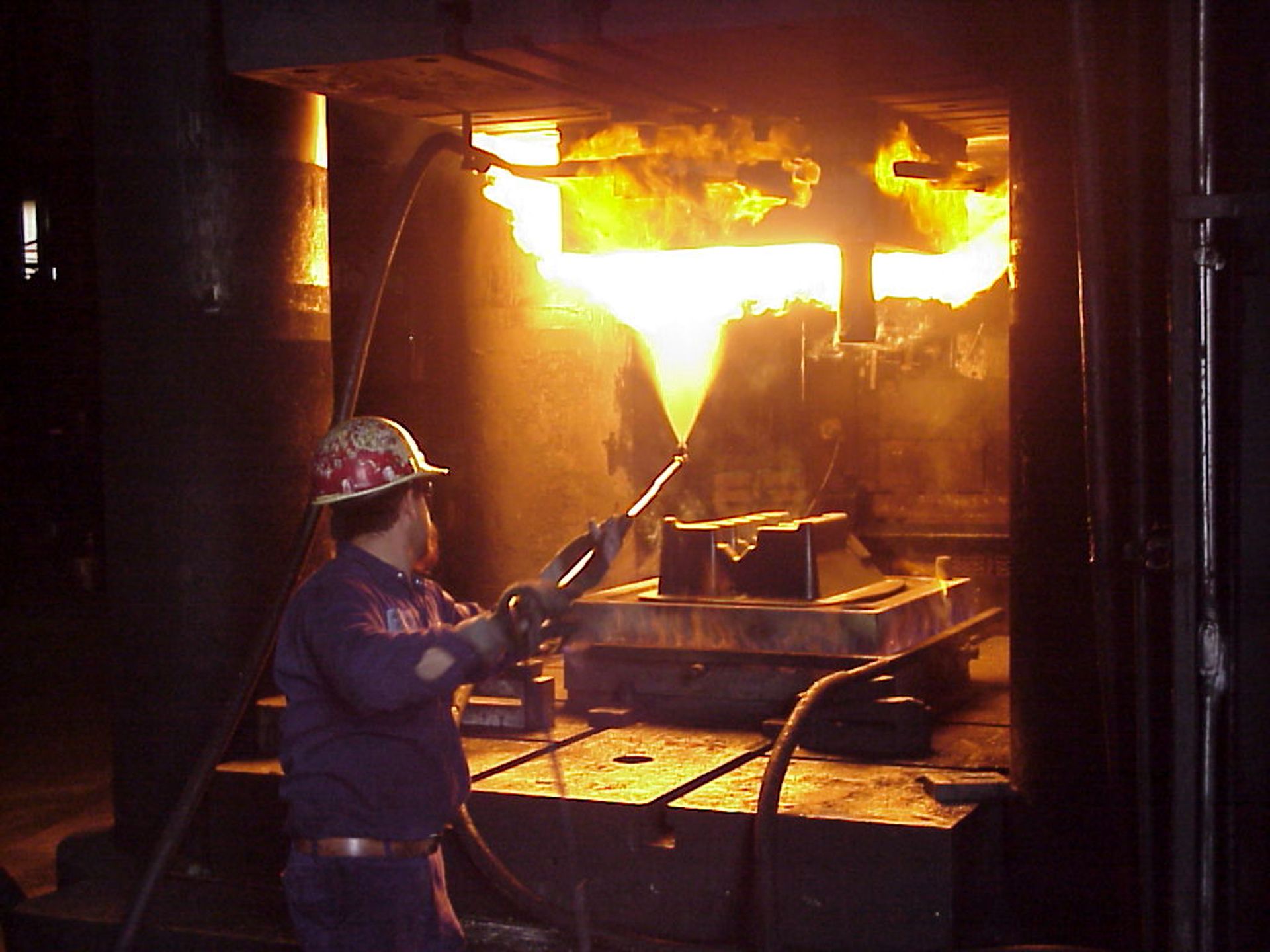
It’s an Outer Rim. Or a Rim Outer. Just don’t call it a Hoop! OK? Now let’s talk about these things. The process has now advanced to the point where they are CNC spin formed out of light yet strong 6061 plate then heat treated giving high strength and the ability to be highly polished and finely brushed. On our Fat Lip profile, the beads, inside and out, are rolled over to create a double wall! These things are stout! But should you ever hit a curb, another car or ? hard enough to damage one (stuff happens), just send the wheel back to us. If it’s minor curb rash, we’ll likely be able to polish it out or do a weld repair to the area and re-finish the outer rim. If it’s really serious we’ll machine the weld out in a lathe then split, remove and replace the outer rim for a fraction of the cost of a new wheel. Or if you ever decided you wanted to add mini-tubs and go wider or whatever, we can just re-rim for you. They used to be made only in the traditional (step lip) profile out of 5052 aluminum which is a work-hardening alloy. It starts off soft enough to be formable and during the spinning process work hardens to it’s finished state. Pretty cool material. Back in the day we all had lowered Chevy Trucks and big ‘ole slammed Impala’s and stuff. Some of which didn’t quite have enough (or any) C-notching done to the frame rails to give the suspension a place to hide when the train tracks and pot holes came a punishing… well something had to give and sometimes that was the outer rim. Especially if the tire pressure was low…Well try that now!
Keeping wheel weight down is a good thing. Especially around the outside. There is a lot of area out there. Ride, handling, acceleration, braking are greatly affected by unsprung and rotational weight. Pick up a big cast aluminum wheel. Some of them are remarkably heavy. To get the outer rim section (and the center section) strong enough given the lower strength of cast aluminum, the thickness goes way up. And cast material can be porous enough that they have to be cast thick just to prevent air from leaking right through the material.
Our Manufacturing Process
Machining: Lathes/Mills. CNC’s are awesome!
We start by chucking our near net shape forgings in CNC (Computer Numeric Control) lathes for drilling. milling and turning. What would we do without computers? We not only use them for design and programming. They control machines that accurately drill, turn, bore and create the face contours of our centers, at constant surface speeds if we want, and hold precise dimensions.
What’s truly rewarding isn’t just doing something, but knowing that you are doing it well!
Even little things. Like running a manual lathe and cranking in a deep cut, engaging the power feed and hearing the motor load up when the tool engages the part. At the right spindle RPM to know you are at the optimum surface speed for the tool you’re using and the diameter you’re cutting. Watching the chips curl and break just as they should, as you see the shine left behind… Then disengaging the feed just before you crash at the end of the cut. Cranking the handles back to start another cut while doing the math in your head to know the next diameter you are going to cut will leave just enough for a good finish pass. Yea, it’s rewarding when you are finally holding a trick, finished part. But the process of getting there can be pretty rewarding too. When done well.
Using a CNC is like doing this with your hands in your pockets. You tell the machine what to do. In it’s language. And it remembers. It can use both hands at once. Three, four, five hands actually. With perfect coordination. More accurately than you can image. Then you tell it how to improve. And it listens.
Finishing & Assembly
Finishing: Polishing, Brushing and Coatings
After CNC machining our polishers go to work! It takes our experienced polishers hours at our polishing lathes and with hand held air tools to bring out that Budnik shine.
Then after pre-polishing, we do the brush finishing. We’ll hand finish the details and pocketing or the entire center section and rim if that’s what our customer asks for.
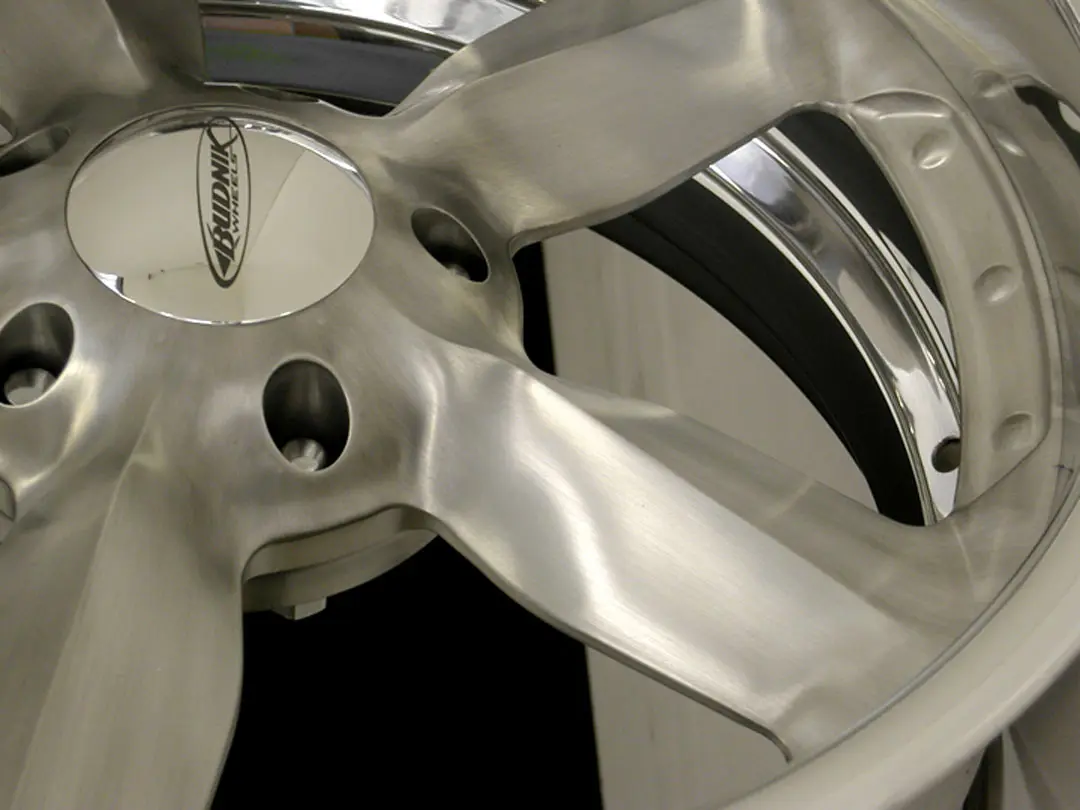
Our ceramic coatings have become very popular. Great colors and a rich, matte finish. A very thin, durable, high tech coating. This is the same stuff that’s used on exhaust headers. We usually coat the entire center section or the entire wheel but we can also mask and coat just the detail milling in the pockets.
We can also provide custom painting to match your color sample and paint code. Powder coating is available too. See our article on the Budnik Custom Finish Process to see more details.
Assembly: The Big Moment
We truly believe our 2-piece Forged and CNC machined wheel construction is the perfect way to build wheels. Strong material so lightweight designs are possible. Excellent finish. Unique designs. 100% machined centers so no unbalanced thick/thin sections as with castings. And assembled at virtually any width and offset to custom fit your unique vehicle or stuff as much tire and wheel as possible under a fender. And they can be repaired or changed by re-rimming.
We assemble to your specs, true, weld, clean and touch up finishes before shipping.